On-Time Delivery Amid Challenges at Century Panels' Kadapa Plant
The demand for Medium Density Fibreboard (MDF) and laminates in India is on a rapid rise, driven by urbanization, increased consumer spending, and a booming real estate sector. As the market for modern, cost-effective materials in furniture and interior design continues to expand, both residential and commercial sectors are fueling this demand. In response, Century Ply, through its subsidiary Century Panels, has significantly expanded its production capacity for MDF and laminate at its facility in Kadapa, Andhra Pradesh. The plant is designed to produce 360,000 cubic meters of MDF and 4.8 million laminate sheets annually, catering to India's growing need for high-quality materials in the construction and interior design markets.
Case Summary
- 01
Challenges
- Monsoon delays caused a 2.5-month setback, hindering initial site execution and equipment movement.
- Severe manpower shortages, with only 30% of civil resources mobilized during critical phases.
- 02
Our Work
- Developed a Focus-&-Finish strategy to ensure clean handovers and avoid premature starts.
- Prioritized MDF plant completion, reallocating resources from the Laminate plant to address civil manpower shortages.
- 03
Results
- Laminate Plant commissioned and operational in 14 months.
- MDF Plant commissioned and operational in 16.5 months, despite significant delays.
This case study focuses on the development and commissioning of Century Panels’ first plant in Kadapa. Realization, a project management firm, was engaged after the major equipment vendors were finalized, although technical specifications were still under discussion. At that stage, site execution had just commenced with the excavation of the first piles. Century Ply’s management aimed to ensure that the entire ₹1,100 crore project would be completed and commissioned simultaneously with the delivery, erection, and commissioning of the major equipment.
The project involved two main production complexes: MDF and laminate, each requiring its own set of auxiliary equipment and utilities. Although the laminate plant could have been commissioned earlier, operating it in isolation would have provided limited business value. Hence, it was deemed essential to complete both plants within the 14-month timeline to ensure maximum efficiency and output.
MDF Production Process
The MDF production process starts with raw wood, which is chipped into smaller pieces. These wood chips are dried to reduce their moisture content and then refined into fibers. The fibers are mixed with resin and wax to form a fiber mat, which is subsequently pressed under heat to create MDF panels. These panels are then cut, cooled, sanded, and inspected for quality before being stored or sent for further finishing.
Key components of the MDF plant include:
- Raw Material Handling: Equipment for receiving, chipping, and storing raw wood.
- Drying Section: A dryer to reduce the moisture content in the wood chips.
- Fiber Processing: Machinery for refining the woodchips into fibers.
- Glue Preparation: Tanks and kitchens for mixing resin with fibers.
- Mat Forming and Pressing: Machines for shaping and pressing the MDF boards.
- Cutting and Finishing: Tools for trimming, sanding, and cooling the MDF panels.
- Dust and Waste Handling: Silos to manage waste and dust from the production process.
- Energy Plant: Power generation systems to support the plant’s operations.
- Utilities: Water treatment, electrical distribution, and cooling systems.
- Storage and Distribution: Facilities for storing raw materials and finished MDF products.
Laminate Production Process
The laminate production process involves multiple layers of paper, which are impregnated with resin and assembled into sheets. These sheets are then pressed under heat and pressure to form laminate panels. After pressing, the panels are trimmed, cooled, and inspected for quality before they're sent for further finishing or storage.
Key components of the laminate plant include:
- Raw Material Handling: Equipment for receiving, storing, and managing paper and resin.
- Impregnation Section: Machinery for impregnating the paper layers with resin and drying the treated sheets.
- Lamination Process: High-pressure presses for bonding the layers of resin-treated paper into laminate sheets.
- Resin Preparation: Tanks and mixers for preparing the resins used in the lamination process.
- Sheet Forming and Pressing: Equipment for assembling and pressing the layers into laminate panels.
- Cutting and Finishing: Tools for trimming the laminate sheets to the desired size and smoothing the edges.
- Dust and Waste Handling: Systems for managing waste materials such as trimmings, dust, and rejects.
- Energy Plant: Power generation systems to maintain continuous plant operations.
- Utilities: Water treatment, electrical distribution, and cooling systems.
- Storage and Distribution: Facilities for storing raw materials and finished laminate products.
Operating these plants at full capacity requires a consistent and reliable supply of electricity and water. This necessitated collaboration with government agencies to support the installation of transmission towers from the nearest sub-station to the Main Receiving Substation (MRSS) on-site. The project also required the construction of over 50 kilometers of pipelines to transport water to a large reservoir within the plant. Both electricity transmission and water supply were integral parts of the project’s scope, and their successful implementation relied on strong partnerships with state government agencies to complete the external infrastructure in tandem with the internal scope.
Each component of both plants played a vital role in ensuring smooth and efficient production. The raw material handling systems ensured that production could run continuously, while the energy and utility systems provided the necessary power and resources to keep operations running smoothly. Waste management and dust handling systems ensured environmental compliance and reduced waste, further contributing to the plants' operational efficiency.
The successful execution of the project was heavily dependent on integrating the production processes and ensuring that all components worked seamlessly together.
REALIZATION’S METHOD FOR ON-TIME COMPLETION OF COMPLEX PROJECTS
Realization employs a method that is radically different from traditional practices.
Every project starts with a plan. It is also well-known that once it goes into execution, things do not pan out as envisaged, due to:
- Sheer bad luck like a force majeure that anyway requires a re-assessment
- Risks that can be anticipated, viz. monsoon periods, festive seasons, harvesting seasons, major changes in scope etc. but the actual impact cannot be known
- Risks that cannot be anticipated,
- Day-to-day delays (scope modifications, rework, estimation errors in planning etc.).
- Capacity constraints (mobilization and skill levels, expert and management capacities, cash flow constraints, material shortages etc.)
And, managing projects is all about how we respond to these occurrences, that disrupt our plans.
There is not much we can do about ‘Sheer bad luck”, except for just facing the consequences and re-strategizing.
The mitigation of risks mentioned in (ii) can be planned for in various ways – planning mitigation actions from before, planning for reduced scope during the risky periods, planning some scope early or late, incentivizing or by simply ensuring buffers in the plan.
The third category is more dynamic in nature. Day-to-day uncertainties hit daily, resources fluctuate all the time and require continuous managerial interventions.
Research on project timelines indicate that the losses that result out of these events could make up to 25-50% of the eventual duration of the project. Somehow, we end up losing much more time than the direct losses incurred due to these small but frequent events, something akin to suffering a death by a thousand cuts.
In theory, these do not seem to be problems that could be difficult to solve with a bit of discipline and due diligence. Let us understand them in a little more detail.
a. Managing day-to-day delays and uncertainties
When delays happen, we try to find ways to make sure that the subsequent activities can still happen as planned. E.g. If the plan was to hand over 4 foundations to mechanical and we get delayed, we start mechanical after handing over 2. That way we can recover the delay by making sure that the subsequent activities can start as planned.
The above essentially says that we could not finish the current scope in the planned duration. However, we would be able to deliver more scope than planned in the next phase.
Apart from the optimism of the approach, the direct cost of doing more in less time is increased coordination. We need more effort to ensure resources do not wait for work or work does not wait for resources. E.g. When we start mechanical after 2 foundations, we have to be vigilant about the remaining 2 foundations lest the mechanical teams sit idle. We also have to ensure that the fabricated material is being staged in the right sequence, lest it so happens that foundation 3 is handed over by civil and mechanical is ready for foundation 4.
Also, when we increase coordination, we lose flexibility. The mechanical head could have put 4 teams (one on each foundation) and finished in half the time, started with one and then ramped up for the rest, or deployed teams on couple of foundations at a time. But now only the last option remains feasible.
As we sink deeper into this approach, it becomes impossible to manage time. Mathematically speaking, when we get into micro-coordination (daily level), the effect of day-to-day uncertainties are so significant that seamless coordination is impossible. 15-20% coordination losses are inevitable.
We, however, have another option available. What instead of trying to make coordination better, we try not to coordinate amongst the different stakeholders? That requires a different approach. In planning, we try to model the handovers. E.g. The Energy Plant has 7 sections, 2 buildings and over 15 foundations of different sizes and complexities. Of these, a couple of structures and foundations take 5 months, the rest, individually, take 15 days to 3 months. Practically, it is possible to do all of them in one go within 5 months in a Focus-&-Finish batch and provide a single clean handover (instead of 20-25 micro-handovers) to mechanical for the erection works. That also provides mechanical with a lot of flexibility in execution. There too, a couple of sections take 6 months to erect, but the rest take somewhere between 1 to 4 months and it is possible to focus and finish the entire erection in 6 months.
However, we cannot practically execute this in Civil, unless the Good for Construction drawings are also handed over in the right way. In turn, the inputs from the vendors and the ordering of the equipment and the creation of technical specifications, also need to follow a Focus-&-Finish handovers in batches.
The strategy for execution is simple – not to manage by dates, but to manage complete, uncompromised handovers. First, it is possible to fully resource-load a single batch, irrespective of the scarcity of resources across the project as the batch is small enough and therefore, avoid large delays. Second, chances of delays at the batch level are lower because uncertainties in only one or two scope items can affect batch durations.
In spite of that if we are faced with delays, we need to honor the handover agreements instead of compromising it and starting the next batch early and getting into the pressure of perfect coordination. Instead, we need to find ways of crashing batch durations now.
This approach also simplifies planning, the absence of frequent coordination changes eliminates frequent re-planning and from an execution standpoint it is much simpler to manage one handover than manage 50 different handover dates. The default rule of execution is simple – Focus-&-Finish every batch, if you can’t, let it wait for better readiness.
However, this approach necessitates avoiding the most popular reaction – postpone crashing decisions, compromise handovers and manage by seamless coordination.
This transition to treating planned handovers as sacrosanct and finding crashing solutions to honor them is the toughest part of implementing this approach.
b. Managing capacity constraints, resource shortages and fluctuations
When resource shortages are faced, we need to make sure that the right work is staffed while negotiating with the respective stakeholder for more. Or we need to support all the available work, while planning to compensate for the shortfall when the promised mobilization happens. These situations happen dynamically. And hence, resource decisions need to be taken dynamically.
We expect that it should be possible to do that efficiently by having a dashboard that tells us the criticality of the work and the requirement and availability of different resources. We expect to take efficient decisions manually. Or maybe, we expect a powerful software to do it for us, provided we keep feeding it the data in real-time. Or, let experienced personnel decide on the fly based on their experience.
Unfortunately, out of these, only the last one is practically feasible. The dashboard never gets made and the data is never accurate enough.
All of them are also mathematically impossible to do.
This is the harsh reality. We just do not know how to do this job efficiently. It is not about individual capability – the human race does not know how to allocate resources efficiently, despite the computing power at our disposal. Whatever decision we apply, however smart it might have been at that moment, it leads to inefficient allocation and >20% longer duration sat a project level. Doing it right dynamically, is just out of the question.
However, when instead of looking at projects as tasks and paths or sequences or chains, if we look at them as “workstreams”, we can get an extra option (some may prefer to call it ‘flow’. This term is used only by Realization and the visibility of workstreams is provided by Streamliner).
Do every workstream as fast as you can – Focus-&-Finish. Wherever you cannot do that, wait for resources to be released or mobilized. It is practically feasible and simple to manage. It is a stable strategy, irrespective of the volatility of the environment. And it is guaranteed to be near the best.
This is practically the simplest, fastest and most efficient way of allocating resources.
Summary of overall difference in approach
What it also means is that we must avoid taking allocation decisions dynamically. In terms of implementing the solution, that is the tougher thing to do.
At Realization, these are the 2 solutions we implement –Focus-&-Finish batches to counter day-to-day delays and Focus-&-Finish workstreams to counter resource shortages.
Implementing this requires modifications in the way projects are planned, and discipline is adhered to in execution, the way contracts are designed, the way projects are reviewed at every management level and how accountability is established.
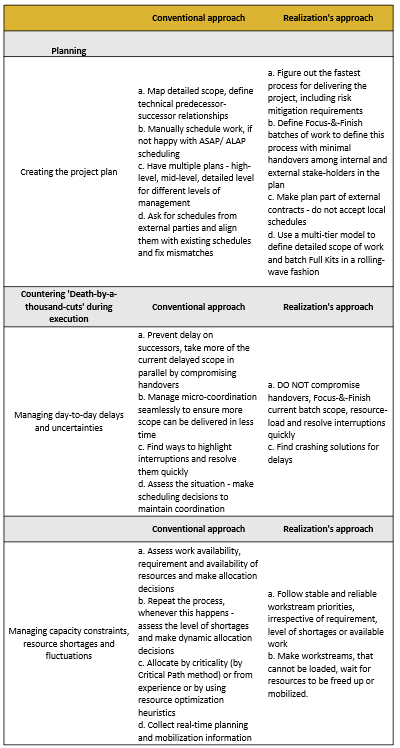
PROJECT EXECUTION AT CENTURY PANELS, KADAPA
The project plan was prepared targeting a 14-month duration for commissioning both the Laminate and MDF plants.
An early jolt
Execution was planned to start in full swing from December, post the retreating monsoons prevalent in the eastern coastal regions of South India. Unfortunately, the monsoons rampaged on for much longer stretching up to end of December. The site located at the base of low hills and the soil type made sure that water would accumulate all over it and the ground conditions made movement of trucks and equipment nearly impossible. This caused the project to start with two-and-a-half months of delay.
Location woes
The site was situated 5 km away from the nearest town, in the middle of almost nowhere and was the sole major project coming up in the region.
Century Panels opted for mobilizing labor contractors for executing the civil scope. Here were not too many local sub-contractors available and the mobilized manpower kept fluctuating right from the start.
Due to the delays in the beginning, the requirement of civil resources had significantly gone up and even with the best of efforts from the management team, only 30% of the requirement could be mobilized between March and July.
The management team went beyond local geographies to mobilize more sub-contractors and were able to ramp up the mobilization to levels of 70%, but only towards the end of the civil works phase.
The usual suspects
Day-to-day delays in designs, modifications in scope, delivery delays, missing material, shortage of scaffolding materials, breakdowns in batching plants, last minute discoveries of missing items etc. events happened just like it happens in any other project.
There were multiple periods – such as Holi, the harvesting season, and Diwali – when manpower levels dropped across the site for a period of 15-20 days and slowed down all work. Additionally, days were lost during the monsoon and retreating monsoons seasons.
The solution
The key was to simply stick to the 2 solution elements inexecution.
A Focus-&-Finish plan (strategy for handovers) was created and agreed upon by all internal stakeholders, right in the beginning.
Agreement was reached on completing batches and resisting premature starts (protecting handovers) and focusing on workstreams in case of unforeseen shortages was reached amongst the management team.
The strategy was discussed and re-drawn after we faced severe shortage in civil manpower and the top management took a decision to de-prioritize the Laminate plant till resources got freed up from MDF.
During execution, in spite of the various delays we faced, the team adhered to the solution elements, resisting the urges to start early and manage through coordination, instead focusing on completing the batch scope in full, resolving emergent issues, ensuring clean handovers and preparing for crashing the subsequent batch(es).
At the time when deployment was only at 30% (and even when less severe shortages were faced during mechanical and electrical works), management team focused and executed only a few of the workstreams, while most of the other workstreams waited.
The results
The Laminate Plant was commissioned and handed over to operations in 14 months and the MDF Plant was commissioned and handed over to operations in 16.5 months.
We started our implementation with Realization in October 2022 for our ₹ 1100 Cr. Greenfield expansion project of MDF and Laminate plants in Kadapa, Andhra Pradesh, when site execution had just started. Along with Realization, we set an aggressive target of 14 months for the production of the first board. Right at the start, the retreating monsoons and its impact on the site, held up work for nearly 3 months.
Due to the location of the project, mobilizing civil manpower was a major challenge. Following the impact of weather, we could only mobilize 30% of the required resources. Apart from these major factors, we faced the usual weather, festival issues, late discovery of scope, delays in drawings and supplies etc. that typically amplifies the delays. Yet, we recovered, and the first board was produced in 16.5 months, only 2.5 months beyond the original target.
Mr. Keshav Bhajanka
Contact us to find out more
Our Customer Service Teams have hundreds of Industry specific studies to draw from ... get in touch if you want to see something specific to your needs, or simply explore how we can deliver Radical Results for you.
Schedule a ‘Top-to-Top’ discussion with one of Realization’s
‘Radical Thinking Officers’.
Set-up a Discussion
Share your contacts and we will set up a ‘Top-to-Top’ meet.